Correct inventory management is key to guaranteeing operational efficiency, reducing costs and avoiding losses in any company. However, many organizations continue to face common errors that affect the accuracy and availability of their products. In this article, we will tell you what the most common mistakes are in inventory management and how you can avoid them through the use of advanced technology and good practices.
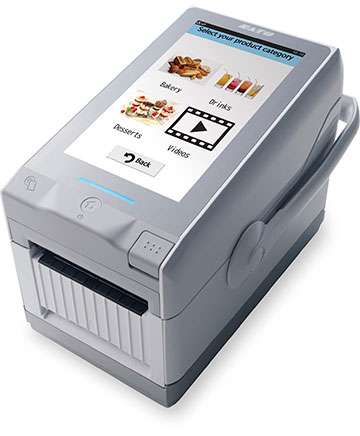
Impresora especializada FX3
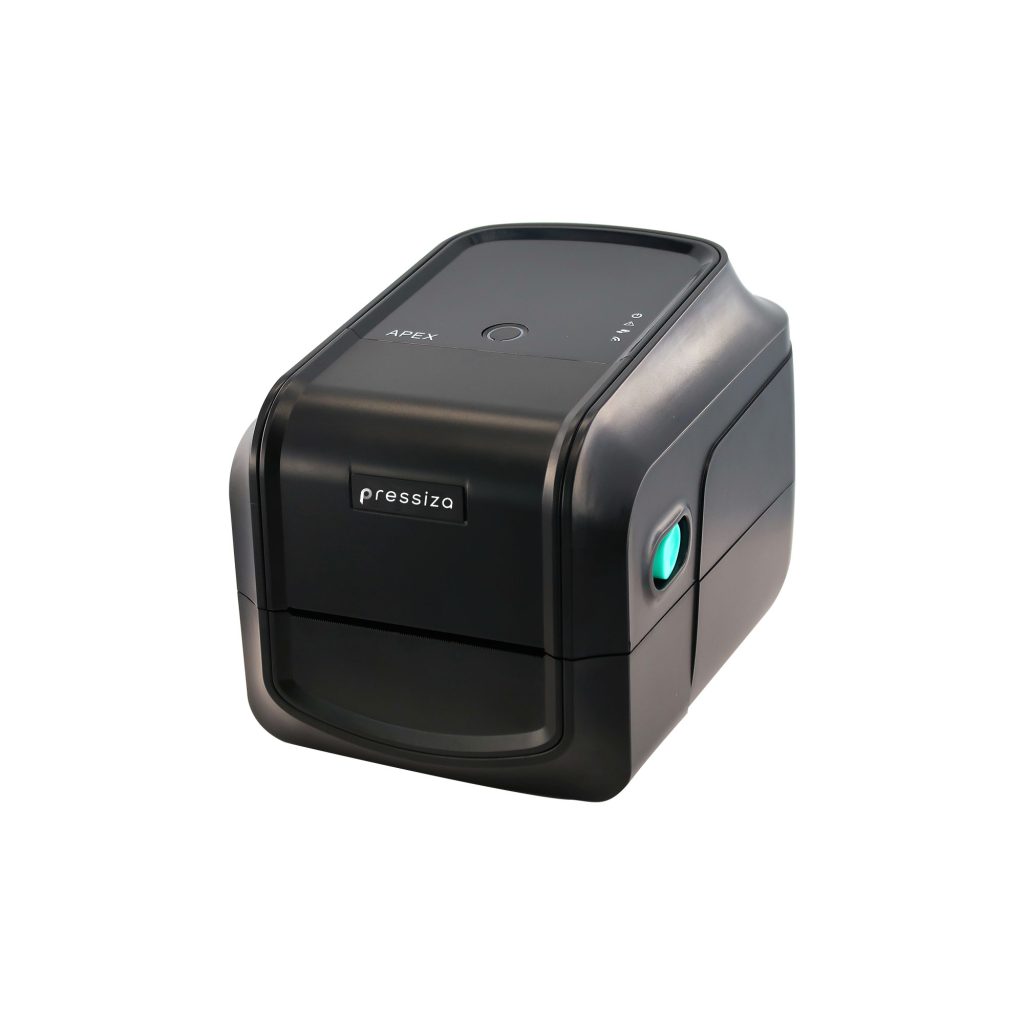
Impresora de trasferencia térmica Pressiza PA-2408T
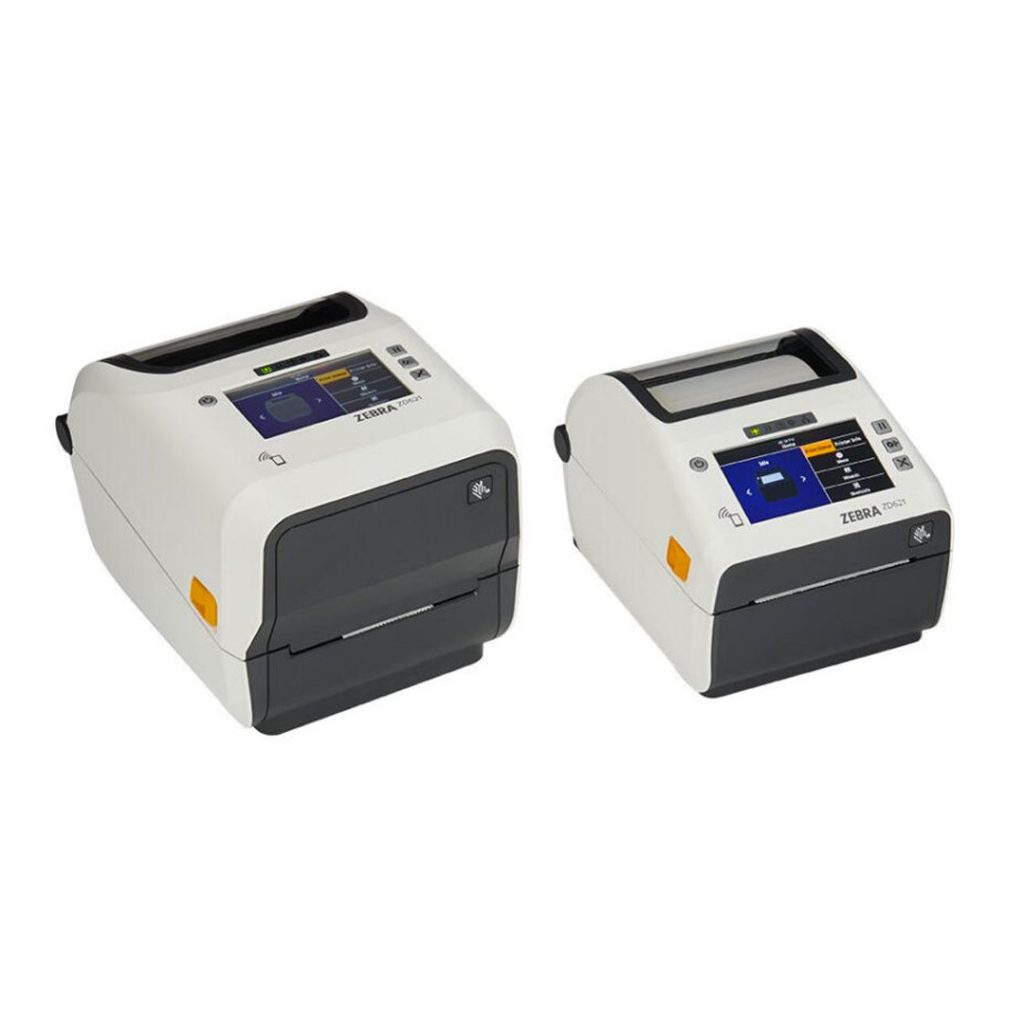
Impresora de escritorio ZD611R con RFID
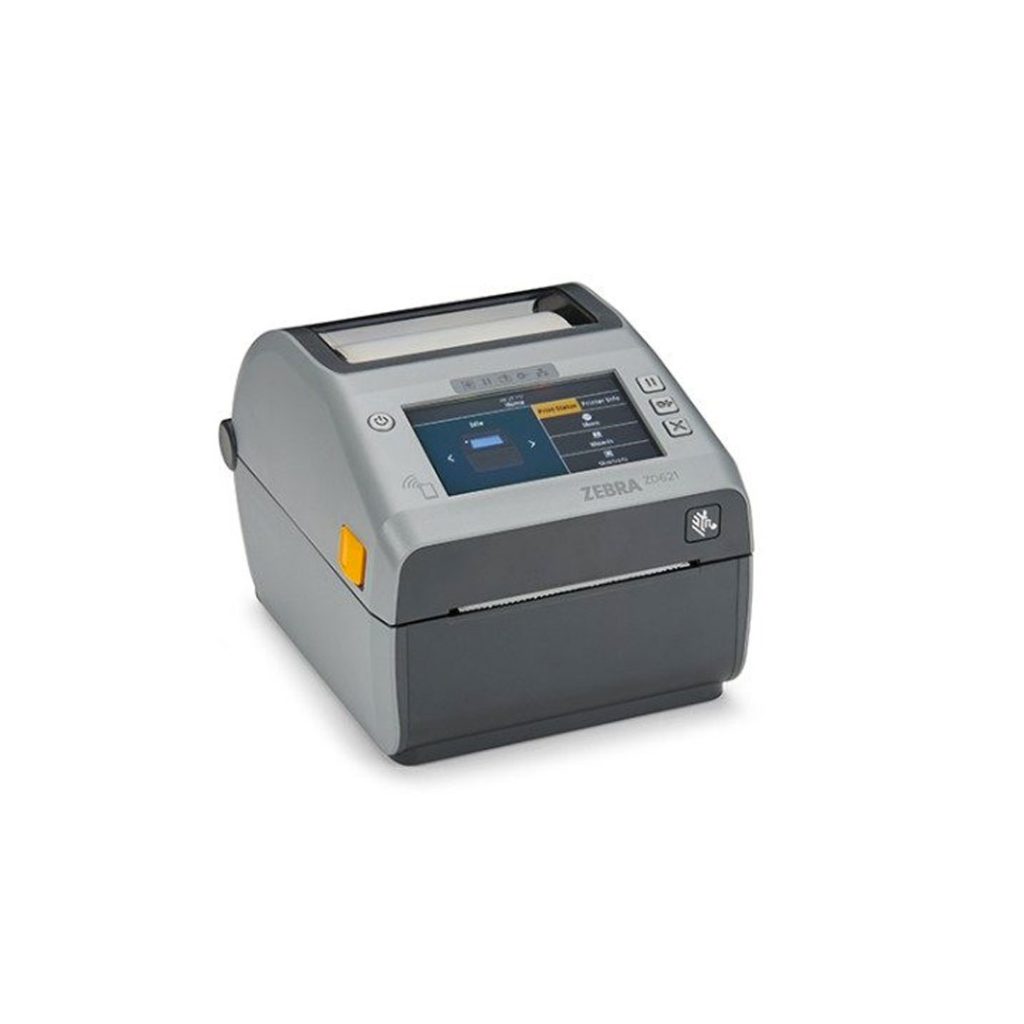
Impresora de escritorio ZD621R con RFID
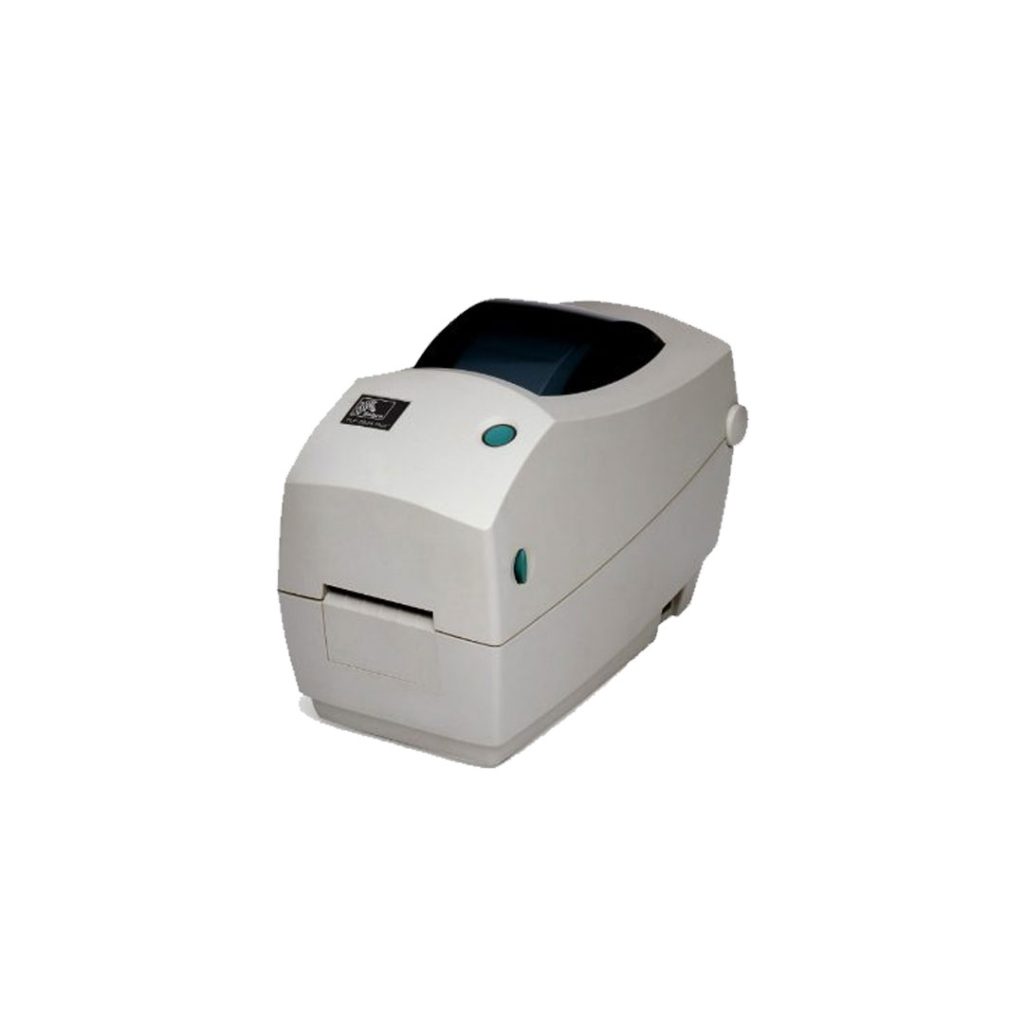
Impresora de escritorio compacta TLP2824 Plus
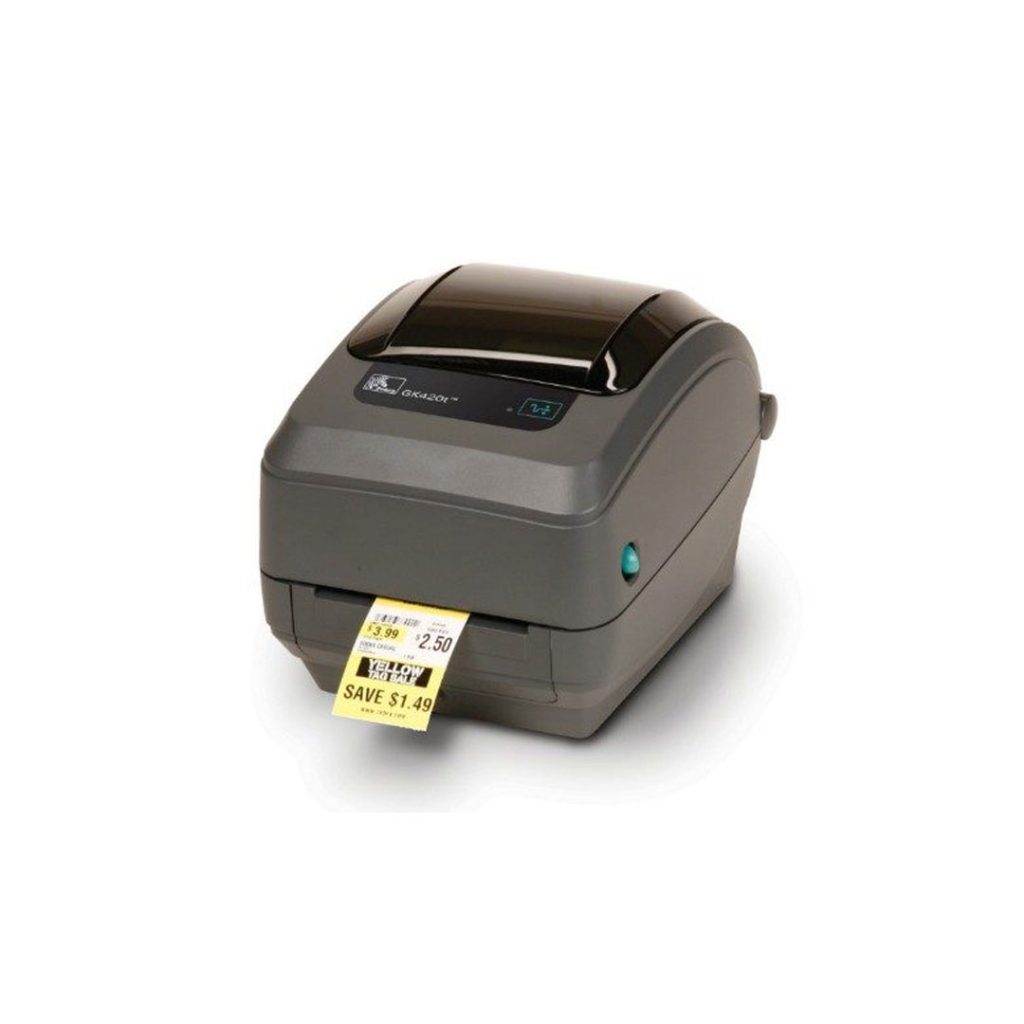
Impresoras de escritorio avanzadas
The most common mistakes in inventory management
1. Lack of control and visibility in real time
One of the most common problems is the absence of a system that allows knowing the status of inventories in real time. This generates mismatches between physical and recorded inventory, causing delays and losses.
How to avoid it?
Implement technological solutions such as warehouse management systems (WMS) or traceability platforms with barcodes and RFID to have real-time control.
2. Manual errors in product registration
Reliance on manual processes to capture inventory inputs and outputs is a constant source of human error, from duplicate captures to incomplete records.
How to avoid it?
Use mobile terminals and barcode scanners that automate data capture and reduce typing errors.
3. Lack of standardized procedures
Many warehouses lack clear policies and defined processes for inventory management, which creates inconsistencies between shifts and work teams.
How to avoid it?
Document and train your staff in standardized procedures and use digital tools to monitor compliance.
4. Lack of knowledge of product rotation
Not identifying which products have greater or lesser turnover can lead to stockouts or overinventory.
How to avoid it?
Lean on platforms that analyze historical data and allow you to implement strategies such as the ABC method to classify and prioritize products.
5. Not anticipating seasonal demand
Ignoring seasonality and projected demand can cause shortages or excess products, affecting the supply chain.
How to avoid it?
Integrate demand prediction systems and keep your inventories synchronized with your ERP or sales systems.
Technology to optimize inventory management
Today, there are tools designed to automate and digitize warehouse management, such as:
- Sistemas WMS (Warehouse Management System)
- Barcode scanners and mobile terminals
- RFID technology for real-time traceability
- Inventory analysis and control software
These solutions not only eliminate errors, but also increase productivity and reduce operating costs.
How can RSI help you?
In RSI Mexico, we are experts in solutions for inventory automation, identification and traceability. We have advanced technology such as WMS systems, mobile devices, RFID and specialized software to optimize warehouse management.
We can help you eliminate errors in your operation, improve efficiency and give you full visibility over your inventories.
Contact us and discover how we can transform your warehouse management.
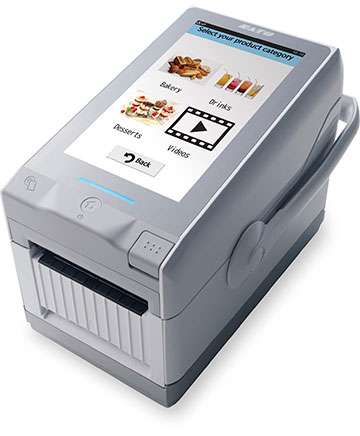
Impresora especializada FX3
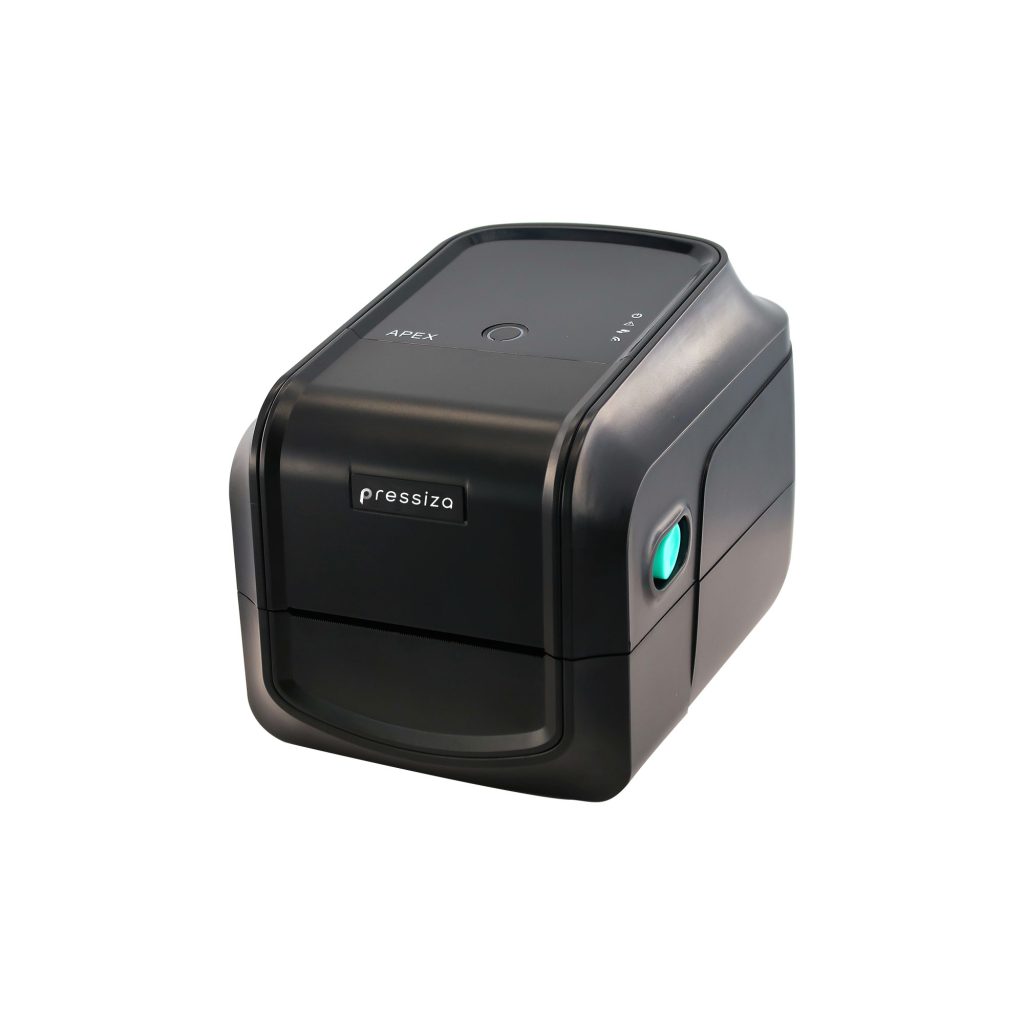
Impresora de trasferencia térmica Pressiza PA-2408T
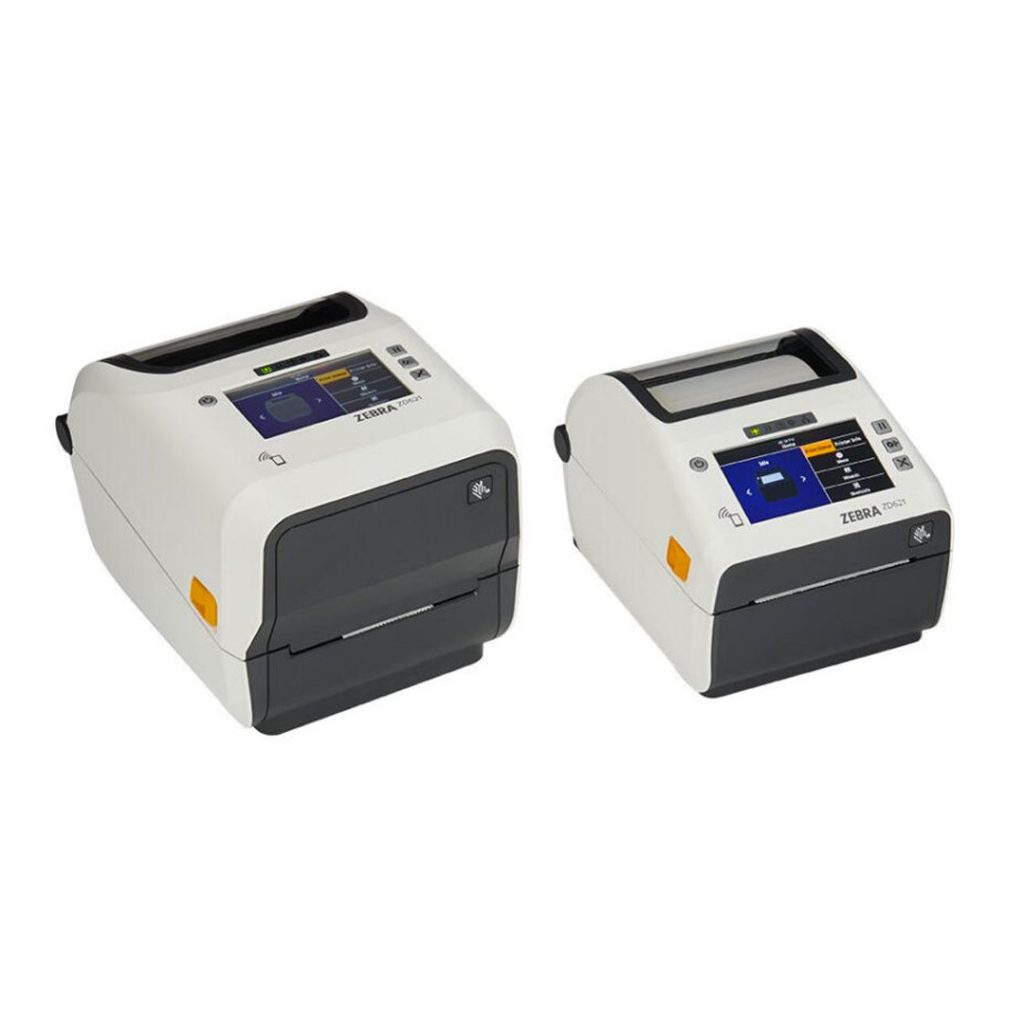
Impresora de escritorio ZD611R con RFID
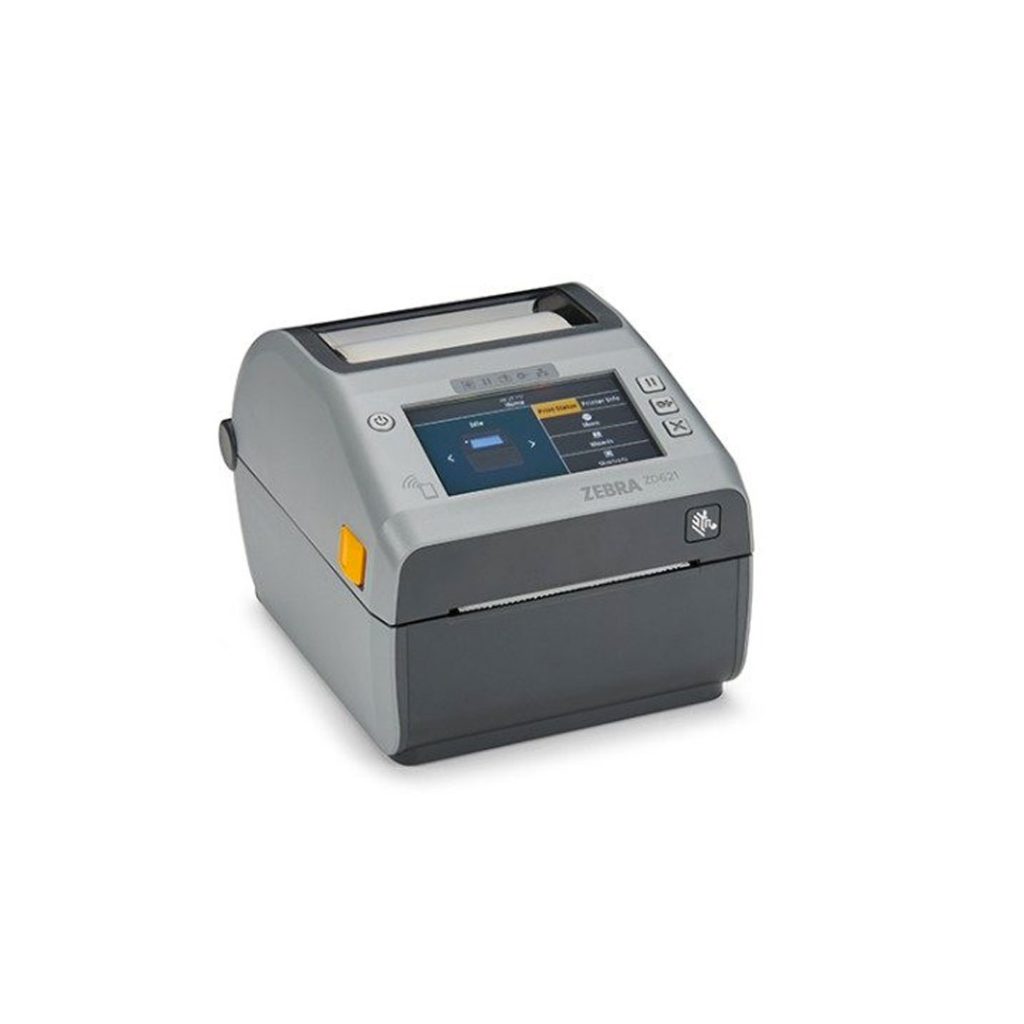
Impresora de escritorio ZD621R con RFID
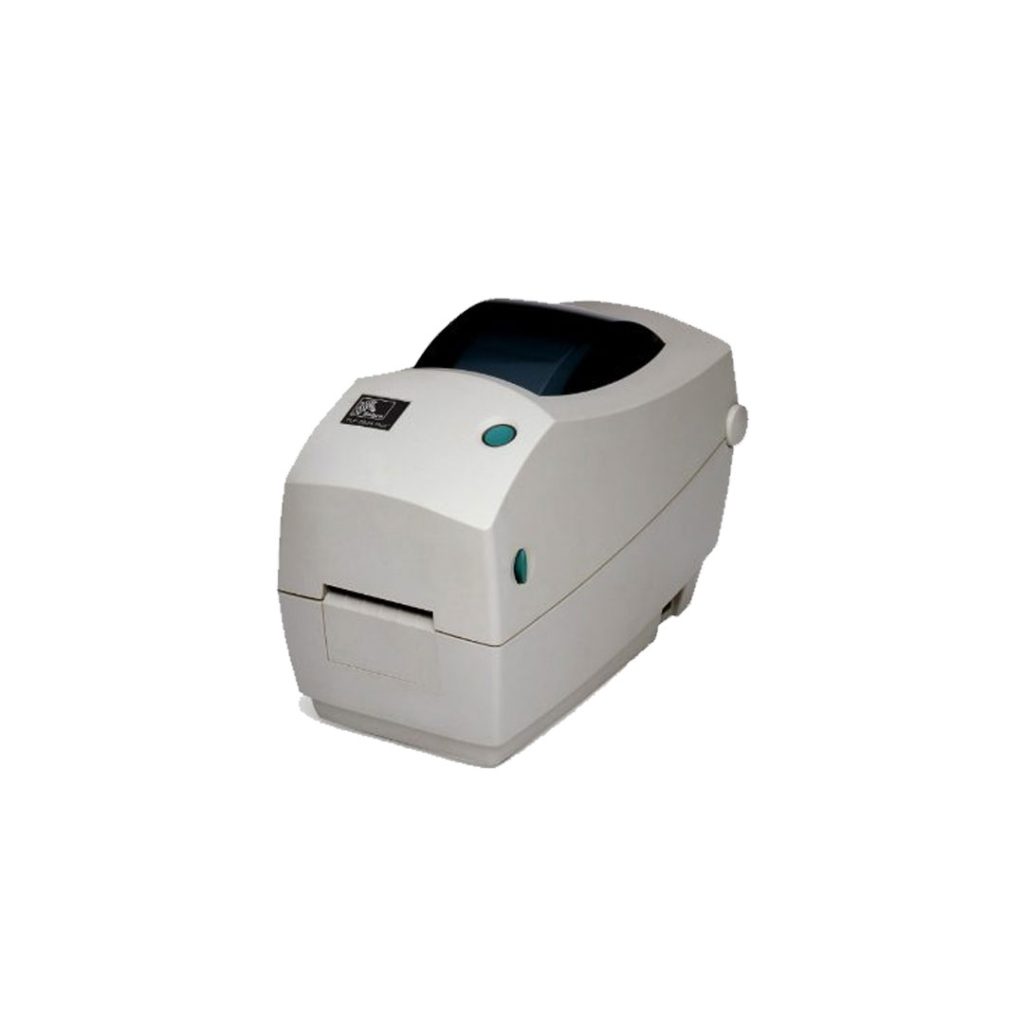
Impresora de escritorio compacta TLP2824 Plus
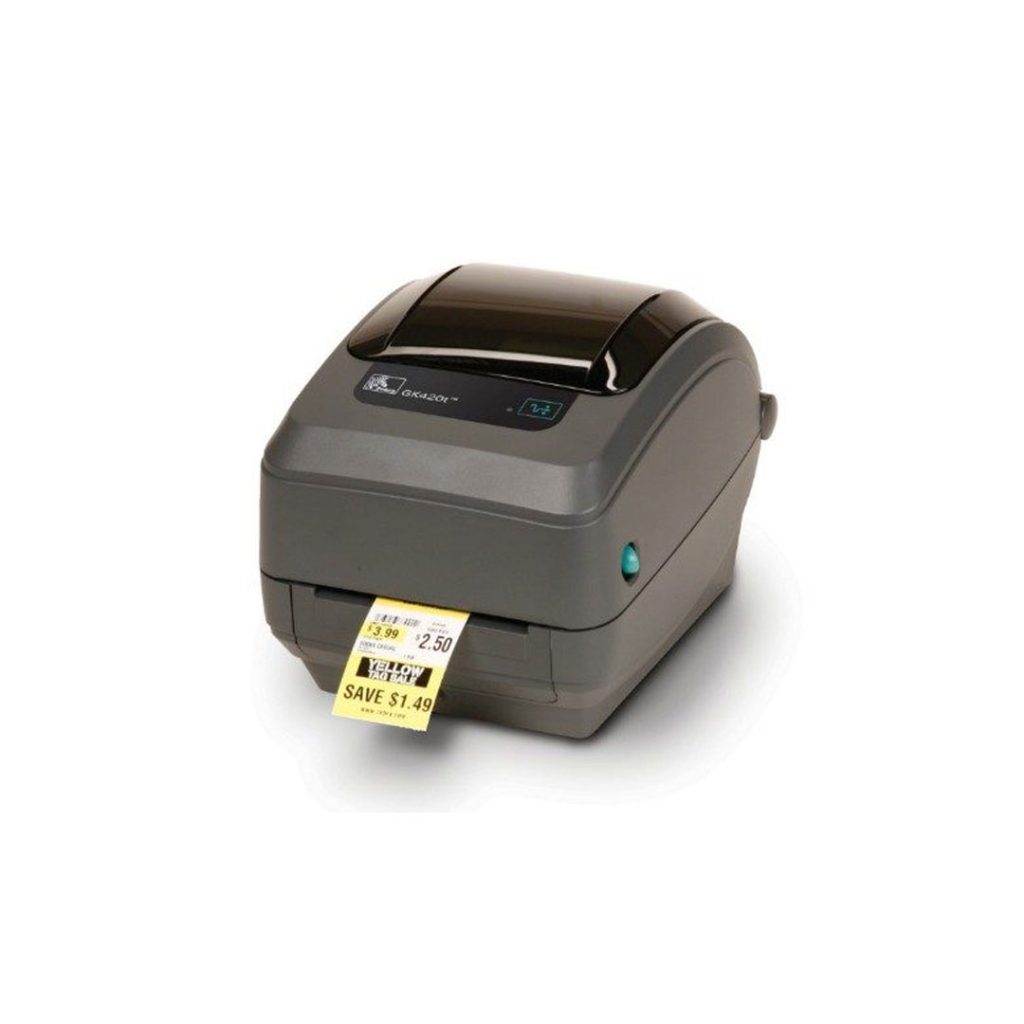
Impresoras de escritorio avanzadas
¿Cuáles son tus necesidades técnicas?
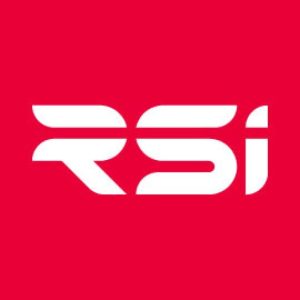
Andrés Alcantara
Especialista en Marketing digital